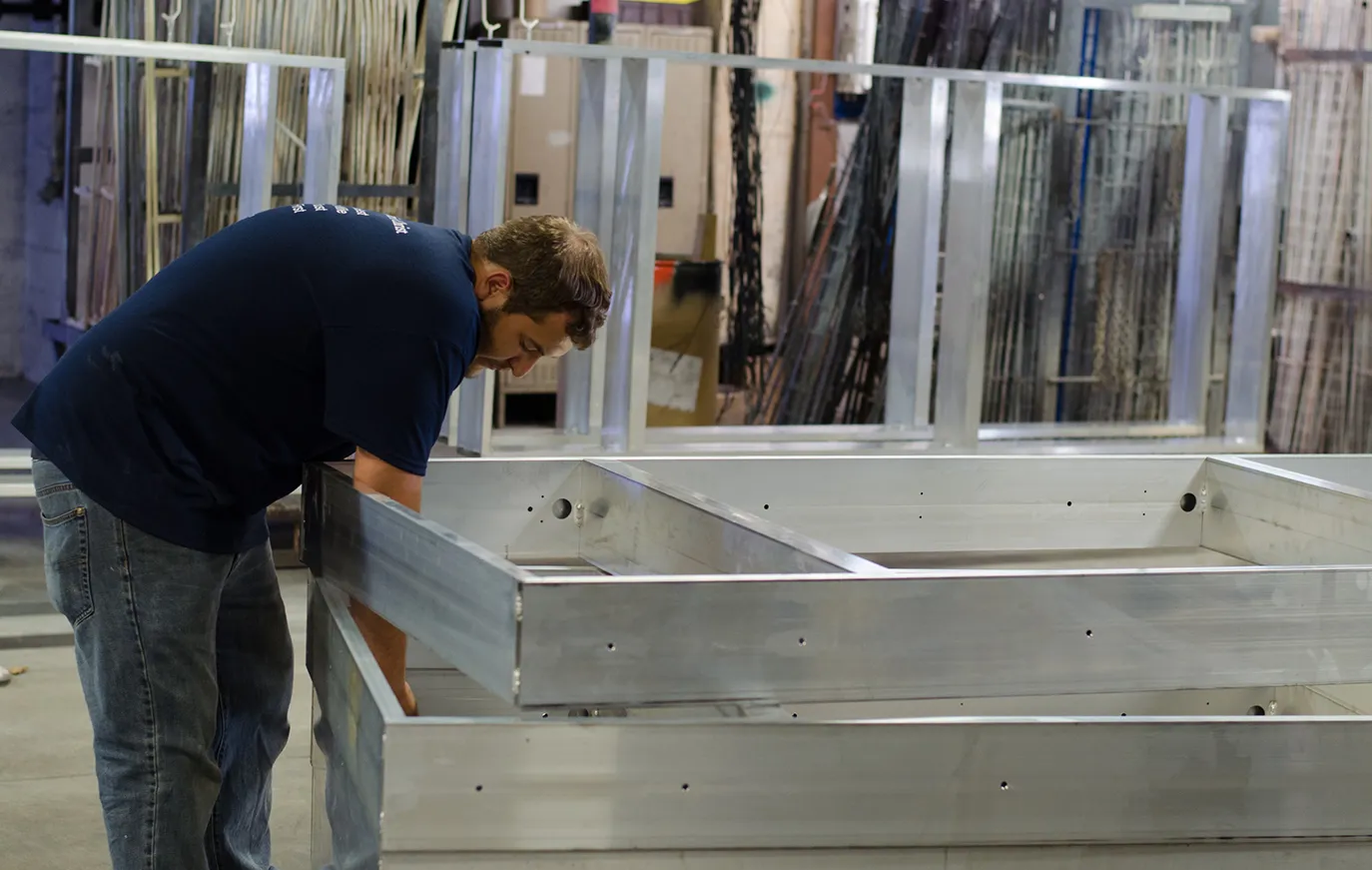
The answer is: yes. Sort of.
Technically, iron and steel rust; aluminum corrodes. The bottom line, though, is that any compromised metal surface impedes proper powder coating adhesion.
When aluminum corrodes, there’s a white oxidation that forms on the surface. That creates a barrier. That barrier is a weak spot that impedes adhesion in the powder coating process.
The finish on your metal will look as good as the surface you begin with, so if oxidation has occurred on your aluminum products, care in surface preparation is crucial.
“Oxides have to be removed,” said Nelson Zimmerman, founder of Keystone Koating. “Sometimes that is a small layer and that can be done by sanding, but can be labor-intensive.”
An alternative method is via sand blast, but there are environmental, health and finish concerns because of silica in the sand.
An aluminum oxide blast is the best method for making sure your aluminum product is powder coated properly. Compressed air moves the chemical compound onto the metal product to remove corrosion.
The powder coating finish is ensured even more with Keystone Koating’s proprietary 8-stage pretreatment system (much more effective than a manual pressure washer or 3/5-stage system).
A seal stage is the final stage in Keystone Koating’s pretreatment system.
“The chemistry in the seal stage can differ. Some seal chemistries work better on steel than aluminum,” Zimmerman explained, “so we use a seal chemistry that’s optimal for aluminum.” Aluminum treated in its own pretreat process is better prepared for powder coating.
To confirm proper adhesion, Keystone Koating can perform a boiling water test, which provides more conclusive results. “Boiled water testing provides a quick result that typically indicates if a coating will likely pass the more rigorous ASTM B117 salt fog test,” Zimmerman said.
Keystone Koating’s aluminum oxide blasting, designated pretreat, and proper adhesion testing will add durability to your aluminum products.